Behind the scenes, industrial artificial intelligence is transforming the efficiency and performance of companies. But the bigger picture is the implication for global sustainability.
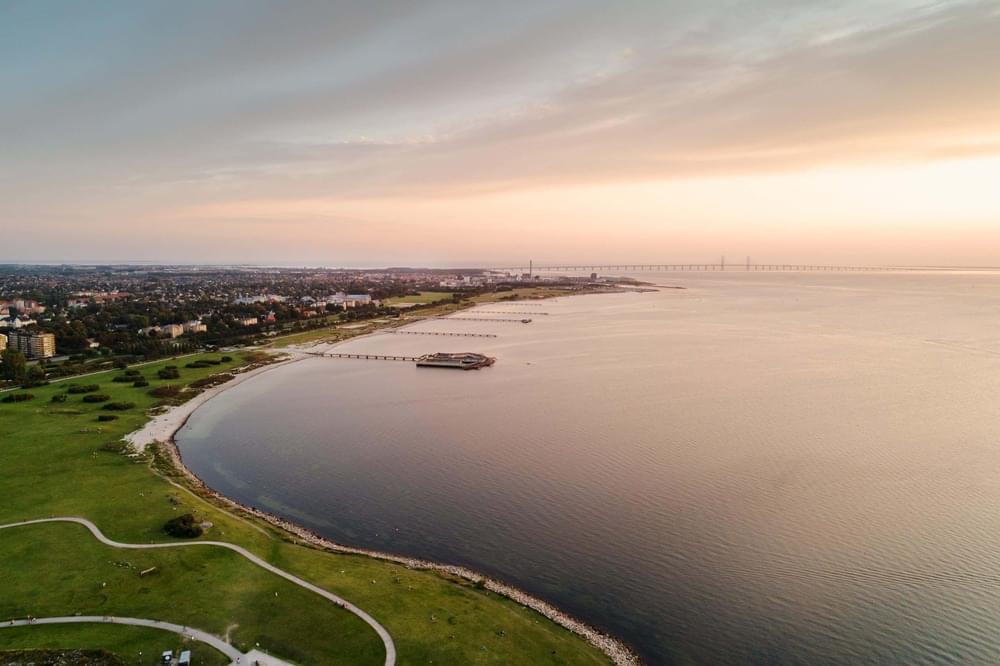
China has installed an 18-megawatt (MW) offshore wind turbine – the world’s largest by power rating – in Guangdong province.
State-owned power generator manufacturer Dongfang Electric Corporation completed the installation of the massive wind turbine at a coastal test base in Shantou on June 5.
China’s 18-MW offshore wind turbine has a 260-meter (853-foot) rotor diameter and a swept area of 53,000 square meters (570,487 square feet) – equivalent to 7.4 standard football fields.
Lab-grown meat, cultivated meat, cell-based meat, slaughter-free meat: All of these terms refer to the process of creating real meat from animal cells, despite names that may allude to a vegan product.
What benefits are there to growing meat from chicken cells rather than raising animals for slaughter? Industrial animal agriculture is responsible for an estimated 15 percent of total global greenhouse gas emissions, and with demand for meat projected to double in the next decade, this technology could offer a more sustainable option for future carnivores.
Come with us as we step inside a lab-grown meat facility, and become some of the first to taste-test chicken that was grown in a bioreactor instead of on a factory farm.
One of Earth’s most consequential bursts of biodiversity—a 30-million-year period of explosive evolutionary changes spawning innumerable new species —may have the most modest of creatures to thank for the vital stage in life’s history: worms.
The digging and burrowing of prehistoric worms and other invertebrates along ocean bottoms sparked a chain of events that released oxygen into the ocean and atmosphere and helped kick-start what is known as the Great Ordovician Biodiversification Event, roughly 480 million years ago, according to new findings Johns Hopkins University researchers published in the journal Geochimica et Cosmochimica Acta.
“It’s really incredible to think how such small animals, ones that don’t even exist today, could alter the course of evolutionary history in such a profound way,” said senior author Maya Gomes, an assistant professor in the Department of Earth and Planetary Sciences. “With this work, we’ll be able to examine the chemistry of early oceans and reinterpret parts of the geological record.”
Japanese electronics company Toshiba has developed a new kind of cobalt-free battery that could lead to cheaper, more sustainable EVs in the future.
The challenge: Road transportation is a significant contributor to climate change, accounting for 12% of global greenhouse gas emissions, so transitioning from fossil fuel-powered cars and trucks to electric vehicles (EVs) is crucial to meeting our climate goals.
The lithium-ion batteries used in most of today’s EVs have several problems, though, and a big one is that their cathodes are made of cobalt, a rare and expensive metal often mined using child labor and environmentally destructive practices.
The pipe dream of carbon capture is one step closer to reality thanks to a Bill Gates-backed startup that is burying bricks made from plants.
The Washington Post detailed a “deceptively simple” procedure by Graphyte to sequester blocks of wood chips and rice hulls, calling it “a game-changer” for the industry, which has been held back by the cost ineffectiveness of other methods.
“The approach, the company claims, could store a ton of CO2 for around $100 a ton, a number long considered a milestone for affordably removing carbon dioxide from the air,” the outlet reported.
Brighter with Herbert.
As the electric vehicle market booms, the demand for lithium—the mineral required for lithium-ion batteries—has also soared. Global lithium production has more than tripled in the last decade. But current methods of extracting lithium from rock ores or brines are slow and come with high energy demands and environmental costs. They also require sources of lithium which are incredibly concentrated to begin with and are only found in a few countries.
Memphis may get most powerful super computer yet.
Memphis, Tennessee, may host the world’s largest supercomputer, the “Gigafactory of Compute.”:
The Memphis Shelby County Economic Development Growth Engine (EDGE), Tennessee Valley Authority (TVA), and governing authorities hold the key to finalizing the project. If approved, it would be the largest investment in Memphis history.
According to Memphis Mayor Paul Young, the city boasts “an ideal site, ripe for investment,” coupled with a skilled workforce that can “keep up with the pace required to land this transformational project, the Business Insider reported.
The supercomputer itself is expected to be a technological marvel. It will be powered by 100,000 Nvidia’s H100 GPUs, currently some of the most sought-after chips in the AI industry, as reported by The Information.
Imagine if the world’s response to climate change relied solely on speculative predictions from pundits and CEOs, rather than the rigorous—though still imperfect—models of climate science. “Two degrees of warming will arrive soon-ish but will change the world less than we all think,” one might say. “Two degrees of warming is not just around the corner. This is going to take a long time,” another could counter.
This is more or less the world we’re in with artificial intelligence, with OpenAI CEO Sam Altman saying that AI systems that can do any task a human can will be developed in the “reasonably close-ish future,” while Yann LeCun, Chief AI Scientist at Facebook, argues that human-level AI systems are “going to take a long time.”
Jaime Sevilla, a 28-year-old Spanish researcher, is trying to change that. It is far from clear whether and how the capabilities of the most advanced AI systems will continue to rapidly progress, and what the effects of those systems will be on society. But given how important AI already is, it’s worth trying to bring a little of the rigor that characterizes climate science to predicting the future of AI, says Sevilla. “Even if AI innovation stopped, this is already a technology that’s going to affect many people’s lives,” he says. “That should be enough of an excuse for us to get serious about it.”